10+ Examples of Process Improvements for Efficient Process Performance
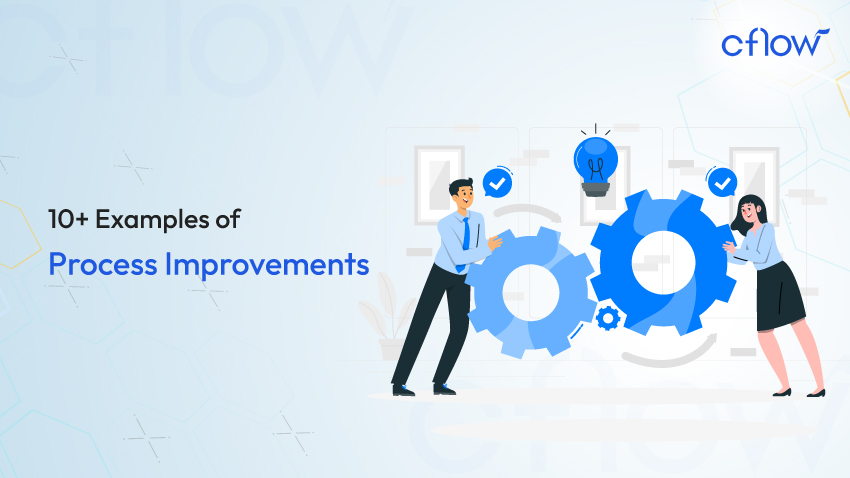
Key takeaways
- The fast paced business environment demands continuous improvement of business processes.
- Every business runs on various processes to achieve a set of objectives.
- All processes need to be reviewed and optimized to improve process efficiency and optimize process outcomes.
- There are numerous ways you can improve a process.
- Lean principles of process improvement focus on eliminating waste and excess processing.
- The main focus of all process improvement examples is to improve service offerings and quality of products, increase production efficiency, and accelerate delivery cycles.
What is Process Improvement?
Business process improvement may be defined as a systematic approach to identifying and improving business processes for productivity, efficiency, and product and service quality. If businesses decided to stay the same and carry out their operations in the same fashion over time, their growth would stagnate and businesses would fail eventually. Read on to know the need for process improvement and top 10 examples of process improvements.
Business process improvement (BPI) can streamline workflows, which enables businesses to adapt to changing business requirements. Business process improvement can be considered as a part of broader management discipline of business process management. Various examples of process improvement aim at reducing communication issues, minimizing wastage, and improving resource utilization. Business process improvements most needed by large and small corporations usually belong to 3 categories.
1. LEAN methodology,
2. Six Sigma,
3. Total Quality Management.
Using these methodologies, businesses can evaluate their current processes and adapt to intents of increasing productivity and streamlining workflows. When workflows are streamlined through process improvements, redundancies are eliminated and workflow efficiency is optimized. Businesses stand to gain several benefits through process improvement initiatives, like faster turnaround times, increased productivity, and the ability to respond quickly to market changes.
Business process improvement initiatives are carried out by companies in different ways, depending on the nature and scope of business operations. Companies can implement process improvement efforts through multiple applications.
Table of Contents
Goals of Process Improvement Initiatives
Process improvement is an important part of larger project management plans. Implementing process improvement requires an iterative approach for examining business processes for making them better throughout the project lifecycle. The goal of process improvement initiatives is to identify and eliminate weaknesses in your business processes.
Why do you need a process improvement plan?
“At least 40% of all businesses will die in the next 10 years… if they don’t figure out how to change their entire company to accommodate new technologies.” — John Chambers, Cisco System
Process improvement initiatives let businesses gain a comprehensive understanding of the problem that is being handled. These initiatives focus more on the root cause of the issue, rather than on one or more of the symptoms. A formal process improvement plan allows teams to better prioritize efforts towards improving on the process. With complete focus on improving the process, too much money or effort will not be spent on making changes that do not add value to the business.
Creating a strategic plan for improving a given process ensures that business operations will be as cost-effective and efficient as possible. Without a process improvement plan, process owners are left with guesswork, trial-and-error, and other inefficient approaches. A formal process improvement plan on the other hand helps establish accountability for improvement initiatives. The plan clearly defines the objectives, responsibilities, and timelines for improvement, and also ensures that all stakeholders are on the same page.
Industry Focus of Examples of Process Improvements in North America
Different regions leverage process improvement in various industries and practices based on specific requirements and economic environments.
North America uses process improvement techniques in the technology, Manufacturing, Healthcare, and Finance industries. Some of the process improvement samples or use cases in various industries include –
- Technology focus and software development implements Agile and DevOps methodologies, Workflow automation, and Big data.
- The manufacturing industry makes use of Lean methodology and Six Sigma models for process improvement.
- In the healthcare industry, patient care improvement is achieved with the help of electronic health records.
- The Finance and Banking industry implements process improvements by using Robotic Process Automation, and Machine learning for fraud detection.
Top 5 Process Improvement Best Practices
As mentioned in the above section, each business chooses process improvement methodologies based on specific business requirements. Lean methodology is among the most popular methodologies that focuses on eliminating wasteful tasks and using resources optimally throughout a given process. Six Sigma methodology is another methodology that is popularly used by businesses to improve quality and reduce defects by eliminating sources of variation throughout a process.
Plan-Do-Study-Act (PDSA) methodology is another cyclical model of continuous improvement that can be implemented in most operational models. Another popular process improvement methodology is total quality management (TQM). This methodology is a customer focused methodology that focuses on data-driven decisions and performance metrics.
Top 5 Process Improvement Best practices include –
1- Align with overall business goals
The most important part of process improvement plan implementation is to align the changes with overall business goals. Seamless alignment with business objectives ensures that they have a positive impact on the company as a whole. You do not want to make any changes to the process without ensuring that the changes would promote financial growth and customer satisfaction.
2- Make specific changes
Specificity is important when planning process improvements. It is important to document all these changes for clarity and consistency in implementing the plan. You must be as specific as possible when identifying the process to be improved, and the manner in which you would like to implement the changes.
3- Ensure data-driven approach
Effective process improvement plans are backed by hard data, which allows teams to take a more objective and critical approach to the initiative. Armed with the right data, teams can uncover hidden issues that may have gone unnoticed otherwise.
4- Involve key stakeholders
Before making even minor changes to the process, the consent of stakeholders is necessary. The key stakeholders need to be aware of the changes and need to be involved in the planning process. Managers and team leads will have a clear understanding of the team’s capacity for implementing the change along with
5- Perform impact analysis
Before implementing the changes to the process, you need to perform a detailed impact analysis that determines the impact of the changes on the process under consideration and related processes.
10 Examples of Process Improvement
Process improvement examples can be categorised based on the focus area of the improvement initiative. Most process improvement examples focus on eliminating waste and reducing costs. Especially the Lean management approach that focuses on eliminating waste producing steps in any process for optimal resource utilization and highly efficient outcomes. Let us look at 10 examples of process improvement.
1. Cost cutting
The most prominent example of process improvement is cost cutting. This can also be considered as a Lean methodology that focuses on waste reduction. Cost cutting can be achieved by restructuring processes, reorganization of operations, and automation of repetitive tasks. Implementing all or some of these techniques can reduce overhead costs significantly. Eliminating unnecessary tasks from the process workflow can eliminate redundancies associated with the process, which in turn reduces costs. Restructuring processes allows for resources to be reallocated so you spend less while your processes flow better. Ways to reduce costs include –
Look for waste in the form of redundant or duplicate tasks
Review the order of execution of tasks within the process and evaluate the material need
Identify opportunities for better resource allocation
2. Visualization of the process
Process modeling allows users to visualize the entire process, which makes it easy to spot bottlenecks and resolve them. Visualization allows users to follow the process and locate delays as they arise, and identify process improvement opportunities that improve its efficiency.
3. Improve collaboration
Another one of business process improvement examples is streamlining the communication process. Process improvement examples intend to improve functionality by streamlining communication by automating the email process or other communication channels. Automating the process decreases the number of emails and contact touch points between departments and employees. This can be achieved using software that streamlines the internal and external communication and sharing of information.
Improving communication and collaboration requires you to eliminate boundaries so that team members can easily share feedback and ideas on a regular basis. The work environment should help people communicate clearly and completely the first time itself so that back and forth communications can be reduced. Using software that automates communication and collaboration by connecting people seamlessly helps in finding answers and getting more work done rather than digging through inboxes.
4. Automating business processes
Automation is the process of using technology for optimizing and streamlining business processes. A workflow solution like Cflow can improve efficiency, accuracy, and speed of customer service, by streamlining the process workflow. Automated workflows can provide significant advantages for businesses of all types and sizes. A process improvement sample is an automation solution that can digitize and automate customer service inquiries so that customers can receive timely responses without being on hold or waiting for an email response from customer service representatives. Cflow automates key process workflows so that process teams can focus on work that adds more value to the business.
5. Continuous Improvement through Kaizen
Process improvement must not be considered a one-time affair, but rather a continuous process. The Kaizen technique focuses on the continuous improvement of business processes. While creating a Kaizen culture within the organization it is essential to maximize business improvement efforts. Kaizen is a Japanese culture that means “change for the better”. The main focus is to make small changes that add up over time to make significant changes. The Kaizen method encourages teams to collaborate and brainstorm solutions for improving existing processes. Encouraging employees to make small but continuous changes that promote an atmosphere of learning and improvement.
6. Minimizing Paperwork
Voluminous paper work eats up a substantial amount of work time of employees. Digital solutions can minimize the paperwork associated with manual solutions. Software solutions can automate paper-based tasks like vendor onboarding or complex requests for quote activities. Businesses can leverage the paperless approach with the help of rules-based routing and digital signatures. Less paperwork also means that employees and managers can find the required information faster, which allows them to complete tasks and projects quickly.
7. Eliminating waste
Waste can be in the form of physical and digital tasks. Physical waste includes excess inventory or materials that can be used more efficiently. Digital waste includes things like redundant data entry tasks or inefficient software programs. For eliminating waste, first areas of resource wastage need to be identified. Once identified, process improvement strategies need to be implemented based on the nature of wastage.
8. Improving visibility and transparency
Having deeper visibility into a process is critical for identifying improvement areas. The right process improvement solution can identify areas of improvement or areas that are delaying the process. Process improvement tools provide visibility and transparency into each step of the process. Business processes in a financial services company require to keep track of regulatory compliance. A compliance management system provides deeper visibility into all compliance activities and reporting, which helps improve overall regulatory compliance and compliance risk.
9. Automate critical documentation
Employees spend a substantial amount of time gathering data and preparing reports. As per a latest survey report, employees spend 1/3rd of their time spend their work hours preparing reports. Employees need to pull data from various sources to prepare spreadsheets and presentations. Although these reports and presentations are important, collating required data manually is an inefficient process, especially when migrating between systems. Organizations that embrace workflow automation carry out data-intensive processes with ease and greater accuracy.
10. Speeding up process cycles
There are several rote steps in processes like employee onboarding, invoice matching, and PO approval. Such processes are full of repetitive steps that do not require human intelligence. These steps can be automated with Cflow so that process cycles are shortened and processes are executed more efficiently. Cflow makes it easy to deliver consistent and streamlined results in a timely fashion. All the required forms, documents, and resources are stored in a centralized location.
End-to-end workflow automation
Build fully-customizable, no code process workflows in a jiffy.
Cflow and Process Improvement Initiatives
In the examples of process improvement mentioned above, workflow automation stands out. A no code, AI-powered workflow automation solution like Cflow makes all process improvement initiatives successful. Cflow is a feature rich automation platform that takes process efficiencies and business productivity to dizzying heights. Lets explore the enterprise-class features of Cflow-
AI-powered workflow tools – You can automate workflows 10 times faster and deliver the best user experience. The all-in-one AI powered platform enables growing and enterprise businesses to automate their workflows without having to write a single line of code.
Workflow templates – Cflow provides 100s of workflow templates for you to choose from. You can choose workflow templates that suit your business requirements and start building workflows immediately. The visual workflow builder in Cflow can be used for building workflows from scratch.
Easy API Integration – You can work with different third-party tools by integrating them with Cflow via APIs. Third-party tools like G-Suite, Office 365, and 1000s of other apps can be integrated with Cflow for higher efficiency and productivity.
Flexible approvals – Cflow allows users to review and approve requests even without a user license. This is the only workflow software in its class to provide this advanced functionality.
Automated routing and notifications – Cflow offers a wide range of options for automatically routing tasks and notifying the concerned individual. This enables timely review and approval of tasks.
Reporting and analytics – All information regarding the status of the requests in Cflow is available to users on the intuitive dashboard. Users can simply glance through to know which requests are pending, make informed decisions, and stay updated on employee productivity.
Data security – Cflow’s secure data encryption allows users to protect sensitive business information. All critical business data is encrypted and role-based access ensures that only authorized personnel can access and edit data.
How Cflow helped SafeSource Direct streamline their procurement Operations
SafeSource Direct is an American-based healthcare equipment manufacturer dedicated to keeping the country’s healthcare sector and workforce safe. SafeSource direct had been facing quality and resource shortage issues since the COVID pandemic owing to the high demand for quality PPE. As a traditionally run business, most of the internal operations were dependent on manual processing. The procurement operations at SafeSource Direct took a hit, which led to delays and interruptions, which ultimately affected customer service. By partnering with Cflow, SafeSource Direct automated their purchase requisition workflow. With Cflow, they were able to fulfill the requests raised by multiple departments in a timely fashion. SafeSource Direct was able to meet the growing demands in the market and produce sustainable products that are safe for the workforce.
How Cflow helped BIC automate their CapEx approval workflows
BIC is celebrating 75 years of making the art of writing accessible to people all over the world with iconic writing and art instruments. As the demand for their products grew and employee count increased proportionally, they required a robust system that supported existing requirements and helped them adapt to changing requirements swiftly. They required an automation system with the capability and reliability to provide solutions quickly and agility to scale rapidly. Cflow provided them with a series of automated workflows that streamlined key processes. The CapEx approval workflows were automated with Cflow for consistent and timely review and approval of all requests.
These were just 2 process improvement samples where Cflow streamlined process workflows for better and efficient outcomes.
Conclusion
Progressive businesses must remain in a state of continuous improvement in order to sustain competition. One common factor among the examples of process improvements listed above is the ability of workflow automation in streamlining core processes. Automating key business workflows is an efficient and effective way to get rid of redundancies and improve overall business productivity.
An AI-powered no code workflow platform like Cflow can be the game changer for businesses looking to improve their process efficiencies and productivity. From small businesses to enterprise level businesses, Cflow offers robust workflow automation solutions for automating core business processes. To explore our versatile workflow automation solution, sign up for the free trial today.
What should you do next?
Thanks for reading till the end. Here are 3 ways we can help you automate your business:

Do better workflow automation with Cflow
Create workflows with multiple steps, parallel reviewals. auto approvals, public forms, etc. to save time and cost.

Talk to a workflow expert
Get a 30-min. free consultation with our Workflow expert to optimize your daily tasks.

Get smarter with our workflow resources
Explore our workflow automation blogs, ebooks, and other resources to master workflow automation.
What would you like to do next?
Automate your workflows with our Cflow experts.