Inventory Management System – What it is and Why Do you Need it? Top 5 Inventory Management Systems
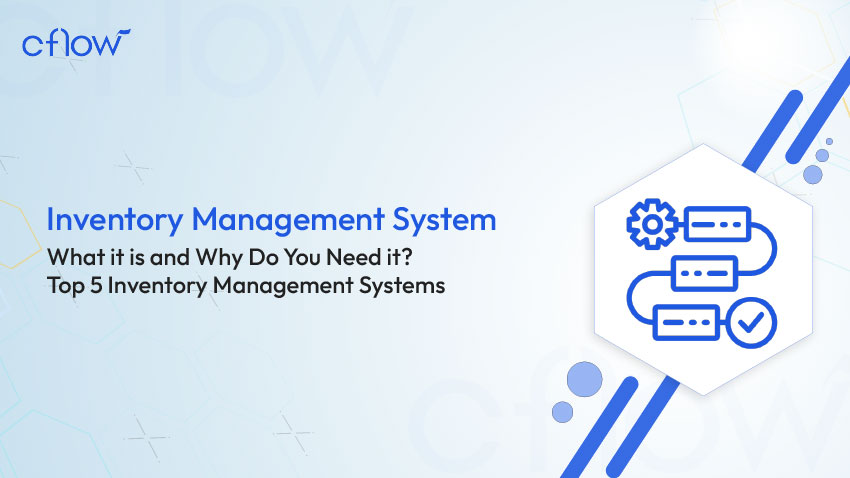
Key takeaways
- An inventory management system is a digital solution that helps businesses track, control, and optimize stock levels. By providing real-time visibility into inventory movements, it ensures smooth operations and cost savings.
- The right inventory management system for small businesses enhances order accuracy, minimizes stock discrepancies, and improves overall supply chain efficiency, making it easier for small enterprises to manage inventory.
- Companies implement inventory management systems to automate procurement, streamline restocking, and prevent issues like inventory shortages or overstocking, leading to optimized warehouse management.
- An inventory management system small business owners can rely on enables seamless integration with sales, accounting, and logistics tools, reducing manual errors and increasing productivity.
- Understanding what is inventory management system, allows businesses to make strategic decisions for stock control, improving forecasting and reducing unnecessary expenses.
What is an Inventory Management System?
An inventory management system is a specialized software tool that helps businesses monitor stock levels, streamline order management, and optimize warehouse operations. It automates tracking processes, providing businesses with accurate, real-time insights into stock availability, order processing, and supply chain performance.
For small businesses, having an inventory management system is vital for maintaining accurate stock records, preventing order fulfillment errors, and reducing operational costs. By eliminating manual tracking, businesses can improve inventory accuracy and ensure a steady flow of products to meet customer demands.
In this blog, we will explore the importance of inventory management systems, how they function, different system types, real-world applications, and factors to consider when selecting an inventory management tool. We will also highlight how Cflow automates inventory management, enhancing efficiency and accuracy.
Table of Contents
Why Do You Need an Inventory Management System?
- Eliminates Manual Errors: Businesses that rely on manual stock tracking often face miscalculations, misplaced inventory, and inaccurate records. An inventory management system automates tracking, reducing human errors and improving accuracy in stock management.
- Enhances Efficiency: Automation speeds up inventory operations, including order fulfillment, stock audits, and supplier coordination. This leads to better productivity and fewer administrative bottlenecks.
- Prevents Stock Issues: Overstocking leads to increased holding costs, while understocking causes stockouts and lost sales. An inventory management system optimizes stock levels, ensuring a balance between demand and supply.
- Improves Decision-Making: With real-time stock insights and data analytics, businesses can make informed decisions on procurement, pricing strategies, and demand forecasting.
- Streamlines Supply Chain Management: Coordinating suppliers, warehouses, and distribution channels is essential for smooth business operations. An inventory system automates these processes, ensuring seamless coordination.
- Boosts Customer Satisfaction: By reducing order delays, preventing stockouts, and improving order accuracy, businesses can enhance customer experiences and build long-term loyalty.
How does an Inventory Management System work?
An inventory management system combines software solutions, barcode scanning, and real-time monitoring tools to automate and optimize stock control. It streamlines inventory-related processes, ensuring that businesses can efficiently manage stock levels, prevent shortages, and reduce waste. Below are the core functionalities of an inventory management system:
- Stock Monitoring: Businesses can track inventory levels across multiple locations, warehouses, or retail outlets. With real-time updates, companies can accurately determine stock availability, reducing the risk of stockouts and overstocking. Stock monitoring also helps businesses maintain a balanced supply chain, preventing delays in production or order fulfillment.
- Order Management: The system automates the process of creating, processing, and fulfilling purchase orders. By automating order workflows, businesses can ensure that suppliers receive accurate and timely purchase requests. This eliminates errors caused by manual ordering, reduces lead times, and enhances relationships with suppliers. Automated order management also helps track pending, completed, and backlogged orders, ensuring efficient stock replenishment.
- Barcode and RFID Integration: Inventory accuracy is significantly improved through barcode and RFID scanning. These technologies allow businesses to efficiently track product movements, scan incoming shipments, and update stock records in real time. Barcode scanning helps with product identification, while RFID technology enables hands-free, remote tracking of inventory, improving warehouse organization and reducing errors in manual entry.
- Inventory Alerts: Businesses can configure automated notifications that trigger alerts for critical inventory-related events. For example, when stock reaches a predefined minimum level, the system can send a low-stock alert, ensuring timely replenishment. Other alerts can notify managers of slow-moving items, upcoming expiration dates, or excess inventory. This proactive approach prevents inventory loss and ensures smooth business operations.
- Reporting and Analytics: The system generates detailed reports on various inventory-related metrics, such as stock turnover rates, demand patterns, and supplier performance. By analyzing historical data, businesses can make data-driven decisions regarding procurement, stock allocation, and pricing strategies. Advanced reporting features help identify inefficiencies, reduce carrying costs, and enhance overall inventory performance.
For small businesses, using an inventory management system can help small business owners easily adapt to simplified stock management, reducing workload while improving inventory accuracy. By implementing automation, small enterprises can optimize their inventory processes without requiring extensive resources, ensuring smooth operations and increased profitability.
Real-life Examples of an Inventory Management System
- Retail Industry: Large retailers such as Walmart use advanced inventory systems to manage thousands of product categories, optimize stock levels, and improve customer service.
- E-commerce Sector: Amazon’s inventory system automates order fulfillment by tracking stock in real time and optimizing delivery routes to ensure fast shipping.
- Manufacturing Industry: Toyota utilizes a Just-in-Time (JIT) inventory system to reduce waste and ensure that production lines receive materials at the right time.
- Healthcare Sector: Hospitals and pharmaceutical companies rely on inventory management systems to track medical supplies, ensuring that critical medicines and equipment are always available.
- Small Businesses: Local grocery stores, clothing retailers, and service-based businesses use cloud-based inventory systems to manage stock, reduce waste, and optimize ordering processes.
Types of Inventory Management Systems
Businesses use different types of inventory management systems based on their size, industry, and operational complexity. Below are the most common inventory management systems, along with real-world examples:
- Manual Inventory System
- This system involves tracking stock manually using spreadsheets, notebooks, or physical records. It is ideal for very small businesses with limited inventory and low sales volume.
- Example: A small bakery manually tracks ingredient stock in a ledger and conducts weekly physical counts to ensure it has sufficient supplies.
- Barcode-Based Inventory System
- Barcode scanners are used to record and track stock movement. Each product has a barcode that, when scanned, updates inventory records in the system, reducing errors and improving warehouse efficiency.
- Example: A clothing retail store uses barcode scanners to track items sold at the checkout counter, updating inventory in real time and automatically reordering when stock runs low.
- RFID-Based Inventory System
- Radio Frequency Identification (RFID) technology enables remote and automatic inventory tracking. RFID tags transmit product data wirelessly to a central system, enhancing efficiency in large-scale inventory management.
- Example: A logistics company tracks packages in transit using RFID tags, ensuring accurate delivery status and preventing lost shipments.
- Cloud-Based Inventory System
- A cloud-based system allows businesses to access inventory records in real time from multiple locations and devices. It integrates seamlessly with e-commerce platforms, accounting software, and warehouse management tools.
- Example: An online electronics retailer manages stock levels across multiple warehouses and updates real-time inventory availability on its website using a cloud-based inventory system.
- ERP-Integrated Inventory System
- This system integrates inventory tracking with Enterprise Resource Planning (ERP) software, providing a comprehensive business management solution. It helps organizations synchronize inventory with sales, finance, and supply chain operations.
- Example: A large manufacturing company uses an ERP-integrated inventory system to track raw materials, manage production schedules, and automate procurement processes.
Choosing the right inventory management system depends on the business’s operational needs, budget, and growth strategy. Companies looking for real-time tracking and automation may opt for cloud-based or ERP-integrated systems, while small businesses with basic inventory needs may find manual or barcode-based systems more practical.
Periodic vs. Perpetual Inventory Systems
Inventory management systems operate using two primary methods: periodic and perpetual inventory systems. Each system has its unique advantages and is suited for different business needs. The table below highlights the key differences between these two systems and provides examples of businesses that commonly use them.
Feature | Periodic Inventory System | Perpetual Inventory System |
---|---|---|
Definition | Updates inventory records at scheduled intervals (monthly, quarterly, or annually). | Continuously updates inventory records in real time with each sale or purchase. |
Stock Tracking | Manual stock counts are required at the end of each period. | Uses barcode scanning, RFID, and automated tracking for real-time stock updates. |
Accuracy | Less accurate due to infrequent updates and potential discrepancies. | Highly accurate as inventory records are updated instantly. |
Technology Usage | Does not require advanced technology; often managed using spreadsheets or basic accounting software. | Requires inventory management software, barcode scanners, and automation tools. |
Cost Efficiency | Lower initial costs but higher risk of mismanagement due to infrequent tracking. | Higher initial investment but reduces long-term losses from stock mismanagement. |
Best Suited For | Small businesses, retail stores, and businesses with low sales volume. | Large-scale retailers, e-commerce platforms, and businesses that require precise inventory control. |
Examples | A small bookstore manually counting stock every month. | Amazon tracking stock levels instantly after each customer purchase. |
Risk of Stockouts | Higher risk as stock is not monitored in real time. | Lower risk since stock levels are continuously tracked and replenished. |
Decision-Making | Decisions on restocking are made after reviewing periodic inventory reports. | Business decisions are made based on real-time inventory data, leading to better demand forecasting. |
Choosing the right inventory management system depends on the nature of your business. Companies that require real-time inventory visibility and automated processes should opt for a perpetual inventory system, while businesses with lower inventory turnover may find a periodic inventory system more practical and cost-effective.
How to Choose the Right Inventory Management System?
- Business Needs: Businesses must assess their inventory complexity, stock volume, and automation requirements to determine the most suitable system. Small businesses may require a simple, easy-to-use solution, while large enterprises might need an advanced system that integrates with multiple supply chain functions. Understanding specific inventory challenges will help in selecting the right software.
- Scalability: The ideal inventory management system should be able to grow with the business. As companies expand, their inventory needs become more complex, requiring a system that supports increased tracking capabilities, warehouse management, and multi-location inventory control. Scalability ensures that the system remains efficient even as the business expands.
- Integration Capabilities: A robust inventory management system must integrate seamlessly with existing business tools such as accounting software, ERP systems, CRM platforms, and e-commerce stores. Integration helps maintain data accuracy across departments, reduces duplicate entries, and ensures smooth operations from procurement to order fulfillment.
- Ease of Use: A user-friendly interface is crucial for ensuring that employees can efficiently manage inventory without extensive training. Complicated systems can slow down operations and lead to errors. Businesses should choose an inventory management system with intuitive navigation, simplified reporting, and customizable dashboards for ease of use.
- Automation Features: Automation is key to improving efficiency in inventory management. Businesses should look for software that offers automated restocking, low-stock alerts, batch tracking, and AI-driven analytics. Automated workflows help reduce manual intervention, streamline stock movement, and optimize inventory planning.
- Budget Considerations: The cost of an inventory management system varies depending on its features, scalability, and integration capabilities. Businesses should compare pricing models, assess ROI, and ensure that the software provides long-term value. While cheaper solutions may have limited features, premium systems often offer advanced capabilities that improve operational efficiency and drive cost savings.
How Cflow Automates Inventory Management?
Cflow is an advanced automation platform that simplifies inventory management by optimizing workflows, reducing manual errors, and improving efficiency. Key features include:
- Automated Stock Tracking: Keeps records of stock movements and prevents inventory discrepancies.
- Cloud-Based Accessibility: Enables real-time inventory tracking from any device and location.
- Customizable Workflows: This allows businesses to create automated approval processes for inventory-related tasks.
- ERP & Accounting Integration: Ensures seamless data synchronization across business tools.
- Inventory Alerts & Notifications: Automatically notifies users about low stock levels, pending orders, and supply chain inefficiencies.
- Advanced Reporting & Analytics: Provides actionable insights to improve inventory decision-making and reduce costs.
End-to-end workflow automation
Build fully-customizable, no code process workflows in a jiffy.
Use Cases of Cflow in Inventory Management
Metier Foods was managing most of their approval processes like new product request, inventory transfer request, and order to delivery, through manual methods. Manual processing of approvals led to delays and errors. They were looking for a solution that could automate their approvals. AI-powered workflows in Cflow automated 25+ processes for Metier foods. The team at metier foods was able to process inventory faster and more efficiently with Cflow.
Blue Bin – a healthcare supply chain management company that offered innovative solutions to streamline medical supplies deliveries. They needed an inventory management system that could manage inventory efficiently and identify process bottlenecks. Blue Bon was looking for ways to overcome the challenges in manual inventory management and streamline the inventory management process. Cflow fits the bill perfectly with its no code, AI-powered workflows. With Cflow, Blue Bin was able to route inventory requests and approve them on time.
1. Cflow – Best for Workflow Automation and Customization
Cflow is an advanced inventory management system that focuses on workflow automation. It helps businesses optimize stock tracking, automate purchase approvals, and streamline order management.
- Key Features:
- Automated inventory tracking and stock replenishment
- Cloud-based access for real-time inventory management
- Customizable workflows for procurement and approvals
- Seamless integration with ERP and accounting software
- AI-driven reporting and analytics
- Pros:
- Highly customizable workflows
- Easy integration with existing business tools
- Scalable for growing businesses
- Cons:
- Requires setup and configuration for advanced automation
2. Zoho Inventory – Best for Small to Medium Businesses
Zoho Inventory is a user-friendly inventory management system designed for small and medium-sized businesses. It provides multi-channel inventory management and integrates with popular e-commerce platforms.
- Key Features:
- Barcode scanning and order tracking
- Multi-channel sales management (Amazon, eBay, Shopify, etc.)
- Inventory forecasting and demand planning
- Integration with Zoho’s suite of business applications
- Pros:
- Affordable pricing for small businesses
- Easy integration with multiple sales channels
- Cons:
- Limited advanced automation features
3. NetSuite ERP – Best for Large Enterprises
NetSuite ERP is a robust enterprise-level inventory management system with advanced tracking, reporting, and automation capabilities.
- Key Features:
- Real-time inventory visibility across multiple locations
- Automated demand forecasting and procurement
- Integration with financial, CRM, and supply chain management tools
- Scalable for enterprise growth
- Pros:
- Comprehensive inventory and financial management tools
- High scalability for large organizations
- Cons:
- Expensive for small businesses
- Requires technical expertise for implementation
4. Cin7 – Best for Omnichannel Retail and Wholesale
Cin7 is an inventory management system built for retail and wholesale businesses, offering multi-channel sales support and automated stock tracking.
- Key Features:
- Omnichannel inventory synchronization
- Automated order processing and fulfillment
- Warehouse management tools
- Integration with POS and e-commerce platforms
- Pros:
- Great for businesses managing multiple sales channels
- Strong warehouse management features
- Cons:
- Higher pricing compared to competitors
5. TradeGecko (QuickBooks Commerce) – Best for B2B and Wholesale Management
TradeGecko, now part of QuickBooks Commerce, is a powerful inventory management system designed for B2B and wholesale businesses.
- Key Features:
- Bulk order management and pricing control
- Integrated accounting and financial tracking
- Multi-location inventory control
- Custom reporting and analytics
- Pros:
- Ideal for businesses dealing with wholesale operations
- Integration with QuickBooks for seamless financial management
- Cons:
- Limited features for businesses outside of wholesale and distribution
Final Thoughts
Implementing an inventory management system is essential for businesses looking to optimize stock control, reduce operational expenses, and enhance supply chain efficiency. Regardless of industry, having the right inventory solution in place ensures that businesses remain competitive in an ever-changing market.
Cflow is the ideal solution for businesses seeking to automate inventory management, enhance operational efficiency, and improve workflow accuracy. Experience the benefits of Cflow and streamline your inventory processes today!
FAQs
What is an inventory management system?
An inventory management system is a software solution designed to track, manage, and optimize inventory levels. It helps businesses automate stock control, prevent shortages and overstocking, streamline order fulfillment, and improve overall operational efficiency.
How does an inventory management system help small businesses?
For small businesses, an inventory management system simplifies stock tracking, reduces manual errors, and improves order accuracy. It enables real-time inventory monitoring, automates reordering processes, and integrates with sales and accounting tools to streamline operations.
What are the key features of an inventory management system?
A robust inventory management system includes features such as automated stock tracking, order management, barcode and RFID integration, inventory alerts, real-time reporting, analytics, and seamless integration with accounting and ERP systems.
How does Cflow improve inventory automation?
Cflow enhances inventory automation by offering cloud-based inventory tracking, customizable workflow automation, real-time alerts, seamless ERP and accounting integrations, and AI-driven analytics. It eliminates manual errors, improves stock visibility, and streamlines approval processes for inventory-related tasks.
What industries benefit most from an inventory management system?
Industries such as retail, e-commerce, manufacturing, healthcare, and logistics benefit the most from inventory management systems. These systems help businesses optimize stock levels, improve supply chain coordination, and enhance customer satisfaction by ensuring timely product availability.
What should you do next?
Thanks for reading till the end. Here are 3 ways we can help you automate your business:

Do better workflow automation with Cflow
Create workflows with multiple steps, parallel reviewals. auto approvals, public forms, etc. to save time and cost.

Talk to a workflow expert
Get a 30-min. free consultation with our Workflow expert to optimize your daily tasks.

Get smarter with our workflow resources
Explore our workflow automation blogs, ebooks, and other resources to master workflow automation.
What would you like to do next?
Automate your workflows with our Cflow experts.