Understanding the Importance of Kanban Board Lead Time and Cycle Time
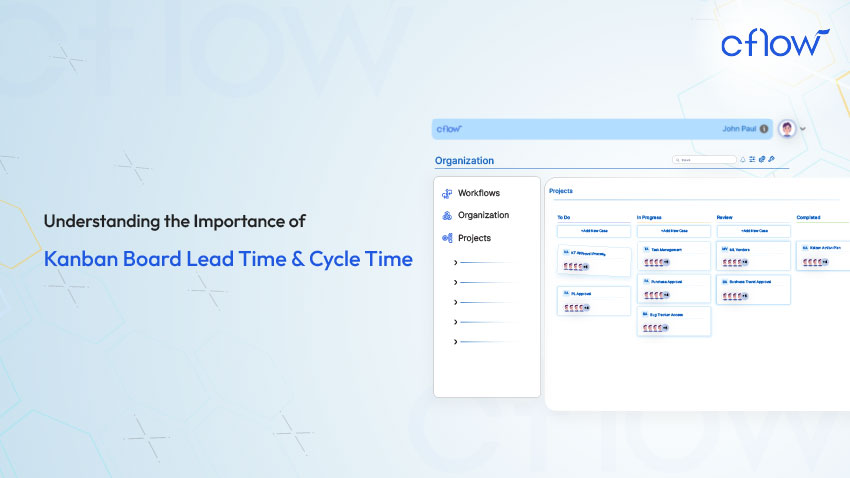
Key takeaways
- Kanban board lead time cycle time are crucial Kanban metrics that help teams track efficiency in workflow management.
- Lead time vs cycle time – Understanding these two metrics improves delivery speed and process optimization.
- Kanban cycle time measures how long a task stays in the system after work has started.
- Lead time represents the total time taken from request to completion.
- Optimizing metrics for Kanban enhances productivity, reduces bottlenecks, and improves team performance.
- Studies show that teams using cycle time in agile reduce delivery time by up to 40% with efficient tracking.
What is Kanban Board Lead Time and Cycle Time?
In Kanban methodology, lead time and cycle time are fundamental metrics that provide insights into workflow efficiency.
- Lead time: The total time from when a request is made until it is completed.
- Cycle time: The time taken from when work begins on a task to when it is completed.
Both cycle time in Kanban and lead time are visualized on a Kanban board, helping teams analyze bottlenecks and optimize workflow. These Kanban metrics are essential for tracking performance, predicting delivery times, and improving efficiency. In this blog we will explore key Kanban metrics, Kanban board lead time cycle time, ways to calculate Kanban lead time and cycle time, and differences between these two metrics.
Table of Contents
Brief on Agile Kanban
Kanban can be seamlessly integrated with agile methodologies to improve team efficiency. Agile practices such as sprints, daily stand-up meetings, and retrospectives can be incorporated into Kanban workflows to enhance collaboration and continuous improvement. Combining agile and Kanban methodologies allows teams to maximize flexibility while maintaining structured progress tracking.
While Scrum follows fixed iterations, Kanban offers continuous flow, making it highly adaptable to changes. Agile teams using Kanban can visualize progress, limit work-in-progress, and maintain a steady delivery pace without the constraints of time-boxed iterations. This flexibility is particularly beneficial for teams working on maintenance and support projects where unpredictable workloads require a more fluid approach.
Exploring Kanban Metrics
Tracking key Kanban metrics within an agile framework enables teams to make data-driven decisions. Continuous improvement is a core principle of agile methodology, and analyzing cycle time, lead time, and throughput helps teams identify areas for optimization. Regular reviews of Kanban metrics allow agile teams to refine workflows, address inefficiencies, and deliver high-quality work more predictably.
By tracking and optimizing these Kanban metrics, teams can ensure a smooth workflow, reduce inefficiencies, and continuously improve their processes for greater productivity and delivery speed. The key metrics for Kanban include:
Lead Time
Lead time captures the duration from task request to completion. For example, if a feature request was made on March 1st and completed on March 10th, the lead time is 10 days. A shorter lead time means that tasks move swiftly through the process, whereas a longer lead time may indicate inefficiencies or bottlenecks. Lead time plays a crucial role in setting delivery expectations and ensuring customer satisfaction.
Cycle Time
Cycle time measures the duration a task remains in progress. If the task started on March 3rd and was completed on March 10th, the cycle time is 7 days. Tracking cycle time helps teams assess productivity and refine processes to achieve shorter turnaround times. A well-optimized cycle time enables teams to complete work faster and meet deadlines more efficiently.
Throughput
Throughput measures the number of tasks completed in a given timeframe. If a team completes 20 tasks per week, their throughput is 20 tasks per week. This metric helps teams analyze workload capacity and forecast project completion rates. Higher throughput indicates a well-functioning workflow with minimal interruptions.
Work in Progress (WIP) Limits
WIP limits restrict the number of tasks in progress at any given time, preventing overload and improving flow efficiency. Setting appropriate WIP limits ensures that team members do not take on too many tasks simultaneously, which can lead to inefficiencies and delays. WIP limits also enhance focus and reduce multitasking, leading to better quality outputs.
Cumulative Flow Diagram (CFD)
A cumulative flow diagram provides a visual for cycle time, helping teams track workflow stability by displaying the distribution of tasks in different workflow stages. A well-balanced CFD ensures that work is flowing smoothly and highlights potential areas of congestion that need attention. It allows teams to anticipate and resolve bottlenecks before they impact delivery schedules.
Flow Efficiency
Flow efficiency measures the percentage of time tasks actively progress versus waiting in a queue. Higher flow efficiency means less idle time in the process, ensuring that tasks move smoothly through the workflow. If a team has a flow efficiency of 60%, it means 40% of the time is spent waiting rather than actively working. Improving flow efficiency helps reduce delays and enhances overall productivity. Flow efficiency is a critical metric in agile environments where speed and responsiveness are key factors.
Blocker Clustering
Blocker clustering identifies patterns in workflow disruptions by analyzing recurring issues that cause delays. By categorizing blockers, teams can develop targeted solutions to minimize their impact and ensure consistent progress. A team that frequently encounters approval delays can address the issue by streamlining review processes and setting clear escalation paths
Lead Time Distribution
Lead time distribution measures the variation in lead times for different types of work items. This metric provides insights into predictability, allowing teams to better estimate completion times based on historical data. Understanding lead time distribution enables teams to set realistic expectations with stakeholders and improve forecasting accuracy.
By tracking and optimizing these Kanban metrics, teams can ensure a smooth workflow, reduce inefficiencies, and continuously improve their processes for greater productivity and delivery speed.
Understanding Lead Time
Lead time captures the duration from task request to completion. A shorter lead time means that tasks move swiftly through the process, whereas a longer lead time may indicate inefficiencies or bottlenecks. Lead time plays a crucial role in setting delivery expectations and ensuring customer satisfaction.
Formula for Lead Time Calculation
Lead time = Completion date – Request date
Example of Lead Time Calculation:
Consider a scenario where a customer submits a feature request on March 1st, and the task is completed on March 15th.
Applying the formula: Lead time = completion date – request date
Lead time = 15 – 1 = 14
Thus, the lead time for this task is 14 days.
Factors that influence lead time include:
- Task complexity: More complex tasks take longer to complete.
- Bottlenecks in workflow: Tasks waiting for approvals or dependencies increase lead time.
- Resource availability: A lack of available team members can extend lead time.
- Prioritization: Low-priority tasks may remain in queues for longer durations.
Reducing lead time enhances productivity, ensures faster deliveries, and improves overall customer satisfaction. By regularly tracking lead time and analyzing workflow data, teams can make informed decisions to optimize efficiency and minimize delays.
Understanding Kanban Cycle Time
Cycle time is a crucial metric that helps teams gauge efficiency in completing tasks. It measures the time taken from the moment work begins on a task until it is completed.
Formula for Cycle Time Calculation: Completion date – start date
Example of Cycle Time Calculation:
Consider a scenario where a team starts working on a task on April 5th, and it is completed on April 15th.
Applying the formula: Cycle time = completion date – start date
Cycle time = 15 – 5 = 10 days
Thus, the cycle time for this task is 10 days.
Why Cycle Time is Important
- Helps in estimating future project timelines: By analyzing cycle time trends, teams can better predict the time required for upcoming tasks and improve planning accuracy.
- Provides insight into workflow bottlenecks: If cycle time is significantly longer than expected, it may indicate inefficiencies in task execution, dependencies, or skill gaps within the team.
- Enables teams to optimize processes for faster deliveries: A shorter cycle time ensures that work progresses efficiently, allowing teams to meet deadlines, deliver quality outputs, and increase overall productivity.
- Enhances team performance: By monitoring cycle time, teams can identify areas for improvement and implement workflow adjustments to maximize efficiency.
- Improves customer satisfaction: Shorter cycle times mean faster delivery of features, bug fixes, and improvements, resulting in a better user experience.
Tracking and analyzing cycle time regularly allows teams to make informed decisions, optimize processes, and continuously improve delivery speed and efficiency.
Difference Between Kanban Lead Time and Cycle Time
Aspect | Lead Time | Cycle Time |
---|---|---|
Definition | Time from request to completion. | Time from work start to completion. |
Measurement | Includes waiting time before work begins. | Measures only active work time. |
Optimization Focus | Reducing delays in the entire process. | Improving efficiency of task execution. |
Impact on Workflow | Affects overall process speed. | Impacts team productivity. |
End-to-end workflow automation
Build fully-customizable, no code process workflows in a jiffy.
Ways to Improve Kanban Lead Time
Identify and Remove Bottlenecks
Bottlenecks occur when work piles up at a specific stage in the workflow, delaying overall progress. By analyzing cycle time in Kanban, teams can identify where work gets stuck and take action to streamline those phases. Techniques such as value stream mapping and cumulative flow diagrams help in visualizing delays and eliminating inefficiencies.
Limit Work in Progress (WIP)
Reducing the number of active tasks ensures faster task completion and minimizes lead time. WIP limits prevent teams from taking on too much work simultaneously, reducing context switching and improving focus. A well-balanced WIP limit allows for a smooth flow of work and prevents unnecessary overload.
Automate Repetitive Processes
Automation helps eliminate manual bottlenecks, reducing lead time significantly. Using automation tools like Cflow accelerates workflows, ensures consistency, and minimizes human errors. Repetitive tasks such as approvals, status updates, and data entry can be automated, allowing team members to focus on more strategic tasks.
Prioritize Tasks Effectively
Organizing tasks based on urgency and importance ensures timely delivery and shorter cycle times. Teams can use priority matrices, Kanban swimlanes, and backlog grooming techniques to categorize and rank tasks efficiently. Prioritization prevents critical tasks from being delayed due to less urgent work consuming resources.
Enhance Team Collaboration
Clear communication and collaboration among team members help prevent unnecessary delays. Daily stand-up meetings, real-time dashboards, and collaboration tools facilitate seamless coordination. When teams share updates and blockers openly, they can resolve issues faster and optimize workflow efficiency.
Improve Task Breakdown and Estimation
Breaking large tasks into smaller, manageable units helps streamline workflow and reduce lead time. Teams can estimate effort levels more accurately and prevent long work cycles that delay completion. Using story points, timeboxing, and task decomposition techniques helps in setting realistic timelines for task completion.
Continuous Monitoring and Adjustment
Regularly reviewing Kanban metrics like lead time and cycle time ensures that teams adapt to changing project demands. Teams should conduct retrospectives and performance analysis to identify areas of improvement and implement necessary adjustments for optimizing lead time.
By applying these strategies, teams can significantly enhance Kanban lead time, leading to better workflow efficiency and increased productivity.
Agile Kanban in Cflow
Cflow enhances Kanban board lead time cycle time efficiency through features like:
- Automated Task Management – Reduces manual delays.
- Visual for Cycle Time – Provides real-time insights into workflows.
- Customizable Workflows – Aligns with Kanban cycle time strategies.
- WIP Limits & Notifications – Helps teams stay within optimal work limits.
With Cflow, businesses can optimize their Kanban metrics to achieve better efficiency and faster deliveries. Process efficiencies can be significantly improved by the Agile Kanban feature in Cflow. Tracking Kanban metrics is simplified with the intuitive dashboard in Cflow. Users can easily track Kanban board lead time cycle time, WIP, throughput, and other important metrics related to processes.
Final Thoughts
Understanding lead time vs cycle time is crucial for workflow efficiency. By tracking and optimizing cycle time in agile methodologies, teams can enhance productivity and improve delivery timelines. Using Kanban metrics effectively ensures a streamlined workflow and better team performance. By leveraging Kanban board lead time cycle time insights, teams can achieve greater agility, faster deliveries, and enhanced workflow efficiency. Agile Kanban in Cflow enables teams to prioritize their tasks and improve process efficiencies. To explore Cflow, sign up for the free trial.
FAQs
What is the ideal lead time for a Kanban board?
Lead time varies depending on task complexity, but shorter lead times indicate better workflow efficiency.
How does Kanban cycle time differ from lead time?
Cycle time in Kanban measures the time a task is actively worked on, while lead time includes waiting periods before work begins.
What is a good metric for tracking efficiency in Kanban?
Key metrics for Kanban include cycle time, lead time, throughput, and flow efficiency.
How can WIP limits improve Kanban cycle time?
WIP limits reduce multitasking, ensuring tasks progress faster and improving overall Kanban cycle time.
What tools can help track Kanban lead time and cycle time?
Tools like Cflow provide real-time visual for cycle time, track performance, and optimize workflows.
What should you do next?
Thanks for reading till the end. Here are 3 ways we can help you automate your business:

Do better workflow automation with Cflow
Create workflows with multiple steps, parallel reviewals. auto approvals, public forms, etc. to save time and cost.

Talk to a workflow expert
Get a 30-min. free consultation with our Workflow expert to optimize your daily tasks.

Get smarter with our workflow resources
Explore our workflow automation blogs, ebooks, and other resources to master workflow automation.
What would you like to do next?
Automate your workflows with our Cflow experts.