Business Process Improvement – What it is, When and Why Do You Need It?
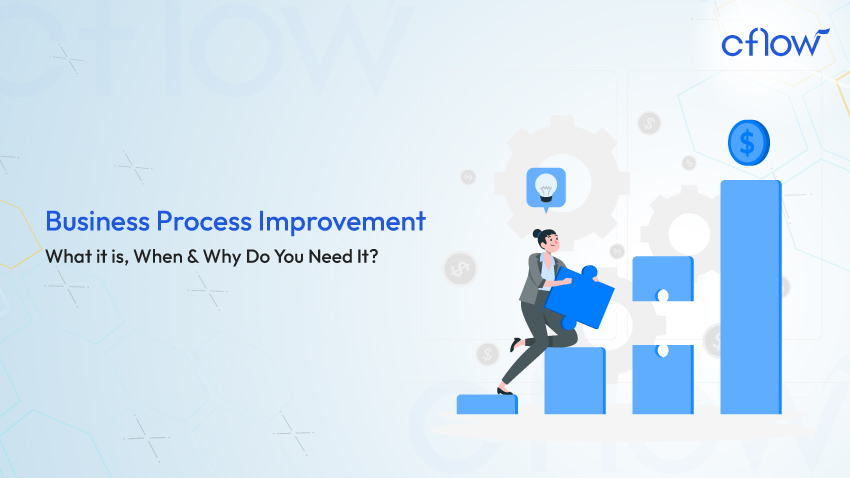
Key takeaways
- Keeping up with continuously evolving markets requires businesses to optimize their business operations.
- Process standardization, quality management, Workflow automation, continuous improvement, and agile methodologies are some of the popular approaches to business process improvement.
- Business process improvement techniques aim at optimizing the underlying business processes so that more efficient results are achieved.
- Among the wide range of business process improvement methodologies, each with different characteristics and use cases, you need to choose the one that is aligned to your business requirements.
- An AI-powered workflow platform like Cflow can elevate your business process innovation efforts to dizzying heights.
What is Business Process Improvement?
Business sustainability and growth is directly proportional to the business process improvement initiatives that it undertakes. What is BPI? Business process improvement includes all those approaches and strategies that a business implements to improve process efficiencies, optimize costs, and improve overall performance. Business process improvements are no longer nice to have, but rather a must-have in the business process management (BPM) strategy.
2023 research projects that the BPM market in North America is poised to reach a whopping 18.26 billion USD by 2033.
North America accounted for more than 40% of the global BPM revenue in 2023.
If you are a business owner looking at sustainable business growth that survives the dynamism of the market, then business process improvement is the most effective way to get there! Read on to understand business process improvement in detail, the benefits of business process improvement, and effective ways to implement BPI in your business.
Table of Contents
Why is Business Process Improvement Important?
Business process improvement brings structure and organization in the efforts undertaken to optimize the underlying processes for achieving better results. All those methodologies that process teams adopt to evaluate current processes and make improvements for increasing productivity may be grouped as business process improvements. From root cause analysis to Lean methodology to change management to continuous improvement – the aim is to analyze existing processes and identify potential for improvements.
So, why do you need business process improvement? Very often business or process owners get into their comfort zone where processes run the way they always have! Not only does this bring redundancy, but also curtails business growth. Progressive businesses always adapt to the dynamism of the market by embracing change. Only when processes are revisited and modified according to current market trends, can the business attain sustainable growth.
Business process improvement need not always be a large scale initiative that involves multiple teams across departments, it could be as simple as value stream mapping or stakeholder engagement, or even employee training and development. Even risk management could contribute to improving business processes. So, you need business process improvement to maintain a steady growth momentum in your business.
You need business process improvement to establish smoother and more efficient workflows. Workflow optimization is the best way you can improve productivity and efficiency. By using process mapping methods, process owners can layout the entire process along with its dependencies in a visual form. This makes it easy to identify bottlenecks and other redundant areas in the process, which can be improved by using appropriate business process improvement methodologies. Business improvement stems from using the right business process innovation that aligns with your organizational goals.
BPI or business process improvement is a great way to eliminate waste and errors from underlying business processes. How? The Lean methodology focuses on eliminating waste from a process, which results in a streamlined process flow. Businesses that adopt this methodology for locate wasteful steps in the process, which can be eliminated. In some processes, there are several repetitive, mundane steps that do not require any intelligence. Workflow automation solutions can automate these steps to save time and money.
Not just at the process level, but BPI can have an impact at the organizational level. BPI initiatives can help an organization establish its practices and workflows with the final goal of creating a business culture that provides high quality customer service. BPI can elevate the current business strategy, vision, and objectives of a business. Enhanced employee morale and customer satisfaction are the byproducts of an improved organizational culture.
Business Process Improvement in Different Industries
Lured by the benefits of process improvement, several industries have implemented BPI innovations to improve the efficiency of process operations. Implementation of business process innovations brings unique benefits to each sector. Let us look at some popular use cases of business process improvement in various industries –
1. Manufacturing
The manufacturing industry can be considered as the pioneer in adopting BPI techniques for eliminating redundancies and wastage from their operations. Manufacturing units harness the power of BPI by implementing Lean and Six Sigma methodologies. The primary focus of both these technologies is to reduce wastage and enhance quality in the production processes.
Take, for example, the ordering process and inventory management. These processes are data-intensive and involve multiple rounds of approval. Traditional processes involve back and forth email exchange between requestors and approvers. When digital automation technologies are integrated into such processes, the lead times and carrying costs are reduced significantly. Automating approval workflows further reduces errors and enhances productivity.
2. Information Technology
This industry utilizes BPI techniques extensively in software development, system integration, system integration testing, and IT support processes. The BPI technique that works best for the IT industry is the agile methodology. This BPI methodology reiterates the importance of continuous improvement and flexibility. Other IT functions like project management, system performance, and customer support, can be streamlined by implementing BPI technologies.
3. Healthcare
The quality of healthcare and patient outcomes can be significantly improved by implementing BPI techniques. Patient admissions and discharge, billing, and appointment scheduling are some of the healthcare processes that are time-consuming and data-intensive. These tasks can be streamlined through workflow automation, which will take care of redundancies and automate repetitive actions. This frees up healthcare providers from mundane tasks, allowing them to focus more on improving the quality of patient care. Efficient patient handling, quicker and accurate billing, and accurate record management are some of the advantages of implementing BPI. Healthcare organizations can adhere to best practices and comply with regulatory standards when they automate healthcare workflows with process improvement techniques.
4. Finance
The finance industry requires very high levels of accuracy in all transactions. Moreover, all financial transactions need to be compliant with financial regulations. Non-compliance attracts heavy penalties for the organization. BPI can significantly improve the accuracy, efficiency, and compliance in the Finance sector, by eliminating redundant processes and improving compliance. Key financial processes, such as loan processing, risk management, and compliance verification, can be automated for greater accuracy and efficiency.
5. Retail and E-commerce
Several processes in the retail sector are repetitive and do not require human intervention. Such processes are better off when automated. When key processes in the retail sector are automated, they are executed quickly and efficiently. Streamlining the processes in the supply chain ensures on time delivery of products from the warehouse to the sales floor. Customer experience is enhanced significantly by implementing BPI for processes related to returns or product exchanges, or customer inquiries.
BPM versus BPI – Key Differences and Similarities You Must Know
The terms business process management (BPM) and business process improvement (BPI) are often used interchangeably. Although BPM and BPI are interconnected methodologies, they differ in their scope and focus. Business process management is a comprehensive management discipline that spans the entire lifecycle of business processes within the organization. The primary objectives of BPM are a holistic approach, continuous improvement, and process definition and optimization.
Business process improvement on the other hand focuses on improving individual business processes. The primary focus of business process improvement initiatives is targeted improvement, data-driven analysis, and short-term focus. BPI is more concerned with individual processes rather than the entire organization. While both BPM and BPI aim at improving operational efficiency, BPM takes a broader perspective by managing entire process ecosystems, whereas BPI focuses on specific processes.
In essence, BPI can be considered as a subset of BPM. BPI focuses on identifying inefficiencies in the current process, proposing improvements, and implementing these changes. Reducing process time, eliminating waste, and improving quality are some of the end goals of BPI initiatives. The overall framework for managing processes is provided by BPM, while BPI is the mechanism that drives the actual improvement within this framework. Both these methodologies work hand-in-hand for managing and improving processes.
Exploring Business Process Improvement Methodologies
What are business improvement techniques? Business process improvement methodologies or technologies can be used by process teams to reduce process inefficiencies and redundancies. In majority of the cases, the BPI methodology you choose depends on the intent behind the improvement initiative and the process you are looking to improve. We will be exploring the top 8 business process improvement methodologies in this section.
1- Lean Methodology
The primary focus of lean methodology is to eliminate waste in all its forms, including time, resources, and effort. Lean methodology is based on the principles of continuous improvement that focus on maximizing customer value and eliminating waste for efficient and simplified processes. Any action that is not required by standards or regulations is considered as wasteful. Such steps or actions do not add any value to the product or service. By identifying waste areas and eliminating actions that generate it, Lean manufacturing helps reduce operational costs.
2-Total Quality Management (TQM)
This is a comprehensive management approach that aims at improving the quality of products and services. Total quality management focuses on creating a culture that transcends all aspects of the organization. Customer satisfaction, continuous process improvement, and commitment of the organization’s collaborators are some of the quality improvement activities that come under the scope of TQM.
This BPI technology focuses on constantly monitoring data to identify deficiencies in the processes that create bottlenecks. TQM optimizes process management process management by streamlining the workflow. Companies that use TQM to improve their processes involve key collaborators in process improvement efforts and encourage their work by developing benefit and recognition plans to reward their actions.
3- Business process reengineering (BPR)
This BPI methodology is a comprehensive and radical approach to business process improvement. BPR involves rethinking and redesigning the way work is carried out within the organization. The ultimate goal of BPR is to achieve radical improvements in the efficiency and effectiveness of the process by reengineering business processes from scratch. Business process reengineering techniques focus on aligning technological processes with business objectives and strategy. Achieving short-term goals by implementing BPR helps businesses increase production levels and streamline process management.
4- Agile methodology
Agile methodology is an iterative and flexible approach towards business process improvement. This methodology lays special emphasis on adaptability, collaboration, and continuous improvement. By implementing agile technology, organizations can quickly respond to evolving customer needs and market conditions by regularly reviewing and adjusting processes. Based on the 4 pillars of the Agile methodology, organizations can improve upon their competitiveness by making processes more flexible and adaptable. The pillars of Agile methodology include –
- Value individuals and interactions over processes and tools used
- Aim at functional software development over extensive documentation
- Collaborate with customers instead of negotiating contracts
- Adapt to change instead of following a rigid plan
Agile methodology primarily focuses on adapting the organization’s processes to market transformation and customer requirements, while staying aligned with the company’s goals and objectives. Business process improvement initiatives that are based on the agile methodology are easily adaptable, interactive, and efficient.
5- Kaizen
With origins from Japanese management methods, Kaizen is steeply focused on continuous improvement. This process improvement methodology focuses on the idea of small incremental improvements that can lead to significant long-term benefits. Kaizen encourages the participation of all employees in identifying and implementing process improvements. This methodology classifies wastes in process management into 3 different categories, namely –
- Muda or waste – Practices that incur expenses but do not add value to processes
- Muri or overload – Any failure of process management that creates bottlenecks
- Mura or discrepancy – Variables or interruptions in workflows that cause overproduction.
This methodology considers that wastes from different categories are related, hence, addressing Muda in a process would result in the subsequent elimination of Mura and Muri.
6- Kanban Methodology
This is also a Japanese management methodology that is related to “visual boards”. Kanban is also an agile methodology that simplifies process management by providing a visual representation that is graphed in columns. In order to apply the Kanban methodology, it is important that different stages of the process are identified accurately. For instance, the management of IT Support requests can be classified into 4 categories.
Pending – This is where requests are placed as soon as they are received, before being assigned to a responsible collaborator.
In progress – This is where requests are assigned to respective collaborators. Requests remain in the “in progress” stage until it is elevated to the next stage.
Scaled up – Once the report is evaluated, it is scaled up to a specialist in the area of error.
Completed – Once the report is resolved, the task is recorded as completed, and the request is ended.
Every task in the process is presented as a movable item that moves from one column to another as the task progresses. Kanban facilitates management of processes by providing a visual representation of processes, which provides control by stages and optimizing the time tasks spent in each column.
End-to-end workflow automation
Build fully-customizable, no code process workflows in a jiffy.
7 – PDCA Cycle
The Plan, Do, Check, Act (PDCA) cycle is a scientifically based methodology. This methodology is designed specifically for problem solving, and comprises 4 steps –
Plan – Identification of the problem to be addressed and devise a solution.
Do – Iteration step where the proposed solution is tested to check its effectiveness.
Check – After implementation of the solution on a small scale, the results are analyzed.
Act – If the results of the previous step are satisfactory, then the solution is applied on a large scale.
The main advantage of the PGDCA cycle is that it minimizes the utilization of resources by testing solutions on a smaller scale at first. After several rounds of testing various solutions, the perfect plan for optimizing its processes before allocating resources to its general adjustments.
8- Six Sigma
This is a data-driven approach that focuses on reducing defects and improving process quality. Six Sigma utilizes a set of quality control and management tools and techniques that can identify and eliminate the root cause of all issues. These techniques finally lead to near perfect results. This methodology is widely used in the manufacturing industry mainly due to its ability to monitor inconsistencies in the production processes. Six Sigma helps make effective adjustments to manufacturing processes to obtain competitive products and services. There are 2 sub-methodologies within Six Sigma – DMAIC and DMADV.
5 Steps for Effective Implementation of BPI
- Identify the process that needs improvement – Conduct a process audit that maps out all existing processes in the organization. Locate the risks and identify areas where mostly needed.
- Analyze existing processes – Look out for bottlenecks and obstacles that hamper process progress. Analyze the current process and performance to determine the quality of results.
- Generate buy in – Build a compelling case and present it to the management validating the need for business process management. The presentation must highlight the impact on performance and customer satisfaction.
- Implement the change – After receiving approval for change, teams need to spring into action. Build a strategy that involves small, but measurable changes. The results of these changes need to be compared now and then, and corrections must be made now and then for accurate resource allocation.
- Fine tune change management – Refine the process changes as needed for achieving optimal results in a consistent manner. You need to keep track of improvements and their impact on the organization.
BPI with No Code Workflow Automation Platforms
Business process improvement through workflow automation produces remarkable results for businesses. Improving business processes with a no code workflow platform like Cflow can make a powerful impact on the business bottom line. As the most trusted AI-powered workflow platform, Cflow can optimize core business processes by eliminating redundant steps. Here is why Cflow is the right business process improvement tool for your business –
- Visual workflow builder
- Conditional logic for request routing
- Drag-and-drop form designer
- OCR for data extraction
- API integration capabilities
- Mobile app for reviews/approvals
- Kanban board functionality available
- WhatsApp integration
- Document designer for PDF generation
To stay on top of business process improvement initiatives in your organization, you need a robust AI-powered workflow automation solution like Cflow.
How Cflow helped BIC pens to Improve their CapEx Approval workflows
BIC pens are a leading writing and art instrument manufacturer with global business operations. With expanding business operations came the need for a robust system that could support expanding requirements. Among their business processes, they were looking to improve their CapEx workflows. The automation system they were looking for needed to support and align with expanding business requirements. Cflow fit the bill perfectly with the no code workflow automation solution capable of automating key process workflows quickly and efficiently.
Cflow provided them with a series of automated workflows that streamlined key processes. The CapEx approval workflows were automated with Cflow for consistent and timely review and approval of all requests.
Key Takeaways
In this blog we have covered key aspects of business process improvement – from what is business process improvement to ways to implement business process improvements to key business process improvement methodologies to choose for your business. Business owners looking to adapt quickly and seamlessly with the dynamism of the market and varying customer expectations need to choose the business process improvement technique wisely. You can rest assured of seamless implementation of business process improvements with an AI-powered workflow platform like Cflow. Ready to explore Cflow? Talk to our experts today.
What should you do next?
Thanks for reading till the end. Here are 3 ways we can help you automate your business:

Do better workflow automation with Cflow
Create workflows with multiple steps, parallel reviewals. auto approvals, public forms, etc. to save time and cost.

Talk to a workflow expert
Get a 30-min. free consultation with our Workflow expert to optimize your daily tasks.

Get smarter with our workflow resources
Explore our workflow automation blogs, ebooks, and other resources to master workflow automation.
What would you like to do next?
Automate your workflows with our Cflow experts.